Flow Wrapper Machine
The Flow Wrapper is a type of packaging machinery used in various industries for wrapping products in airtight packaging. It’s commonly used for packaging items such as food products (like cookies, candy bars, and snack items), medical supplies, hardware, and various consumer goods.
- Variable packages sizes
- Speed control
- Data logging and reporting
- Cutting and sealing mechanism
- Adjustable film unwind
- Pre-labelling option
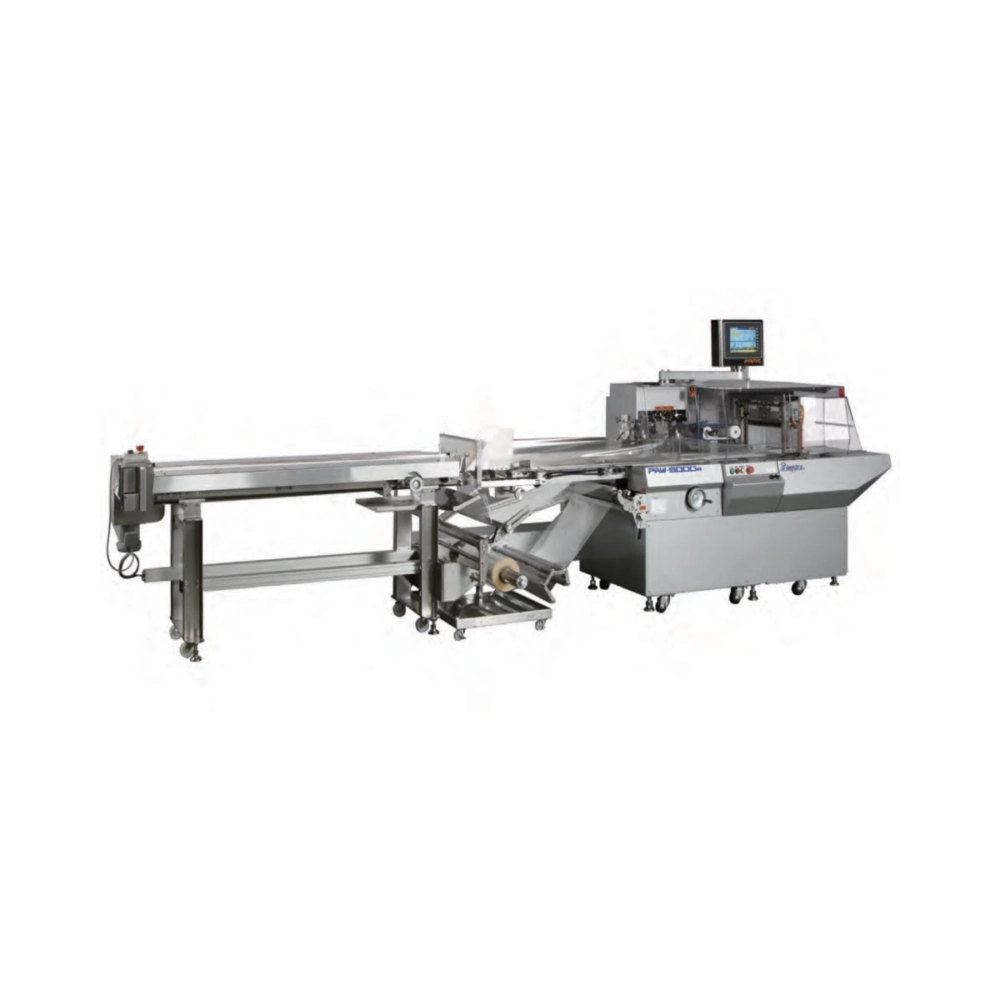
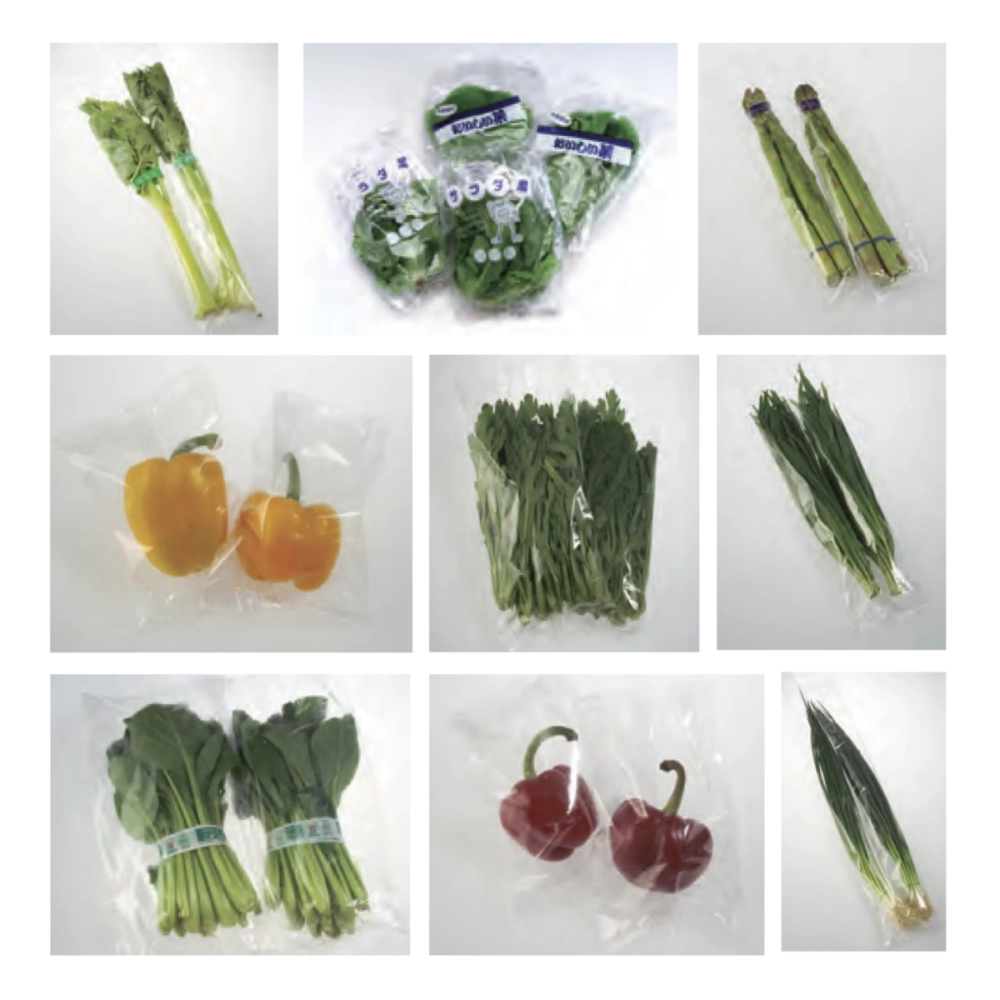
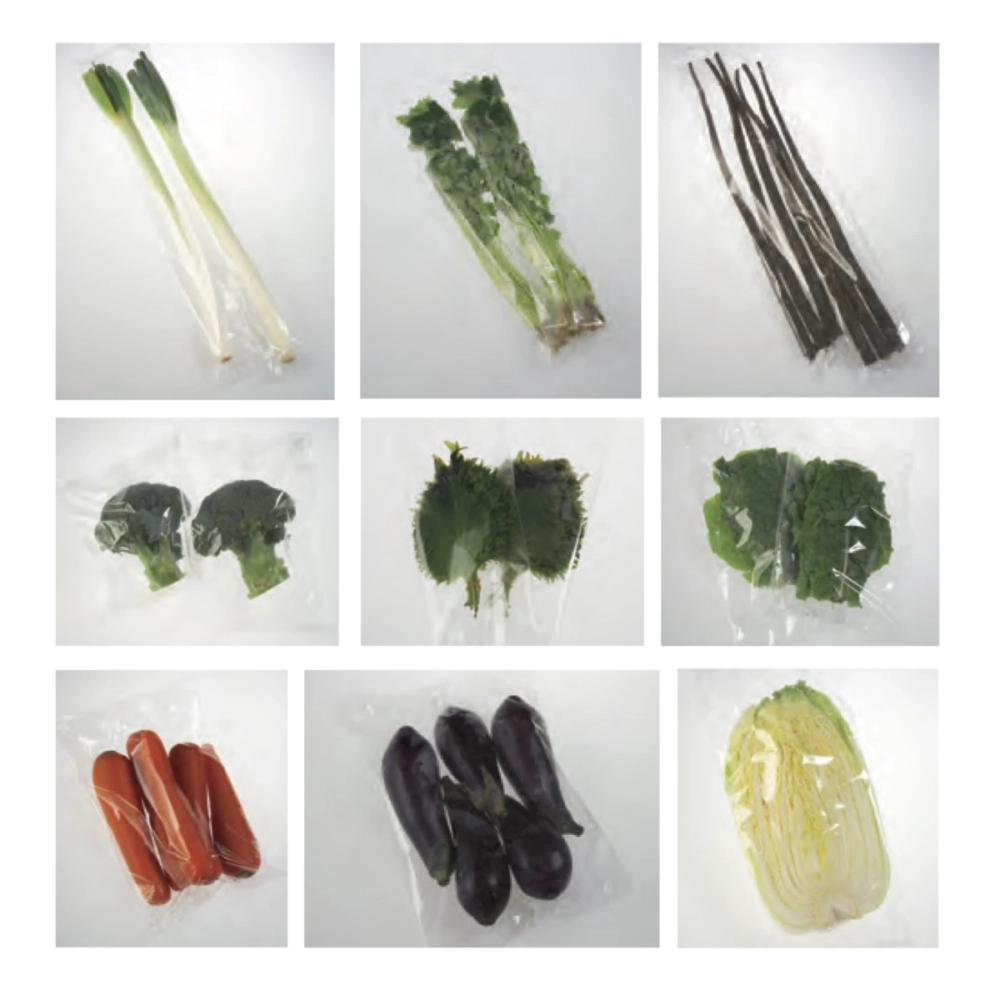
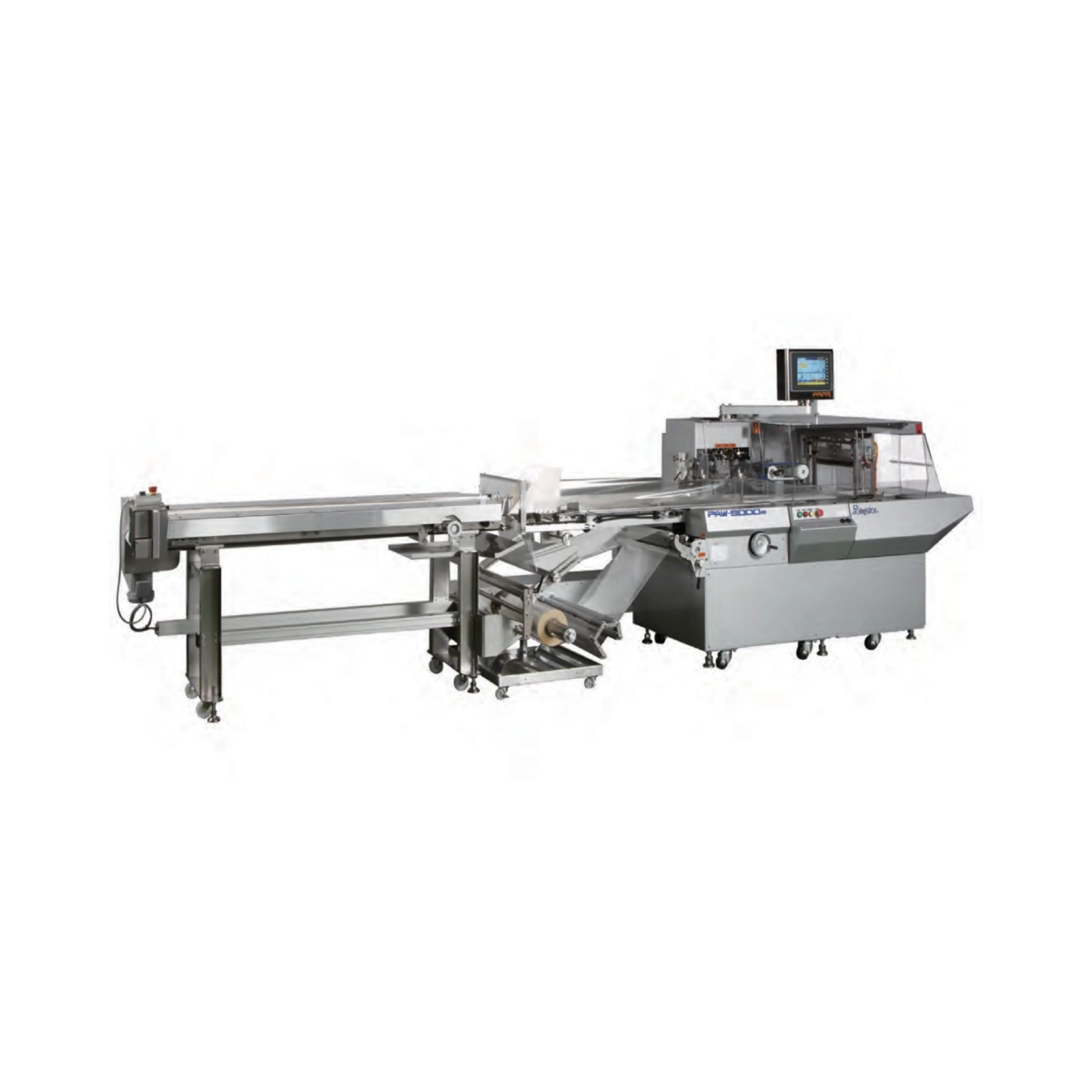
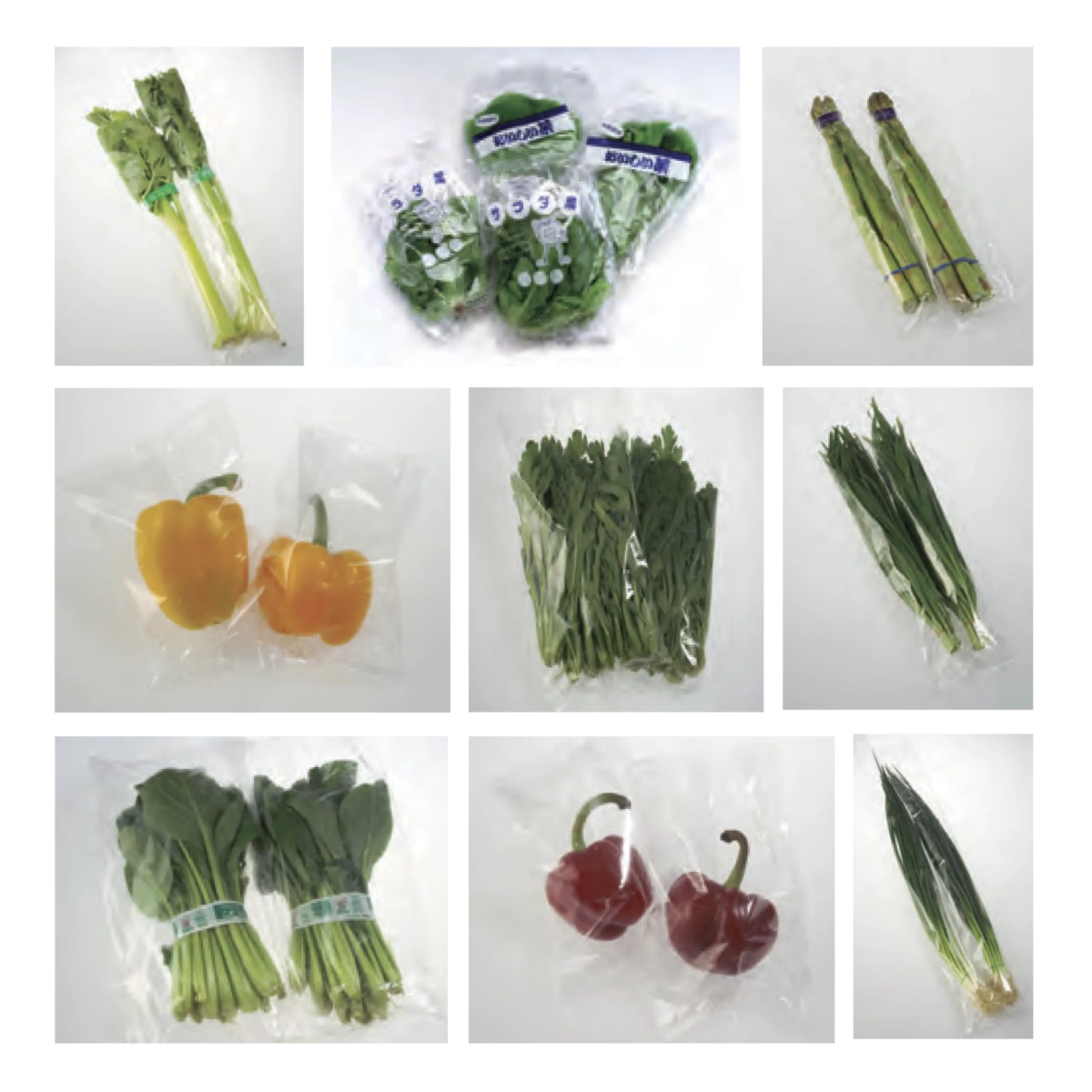
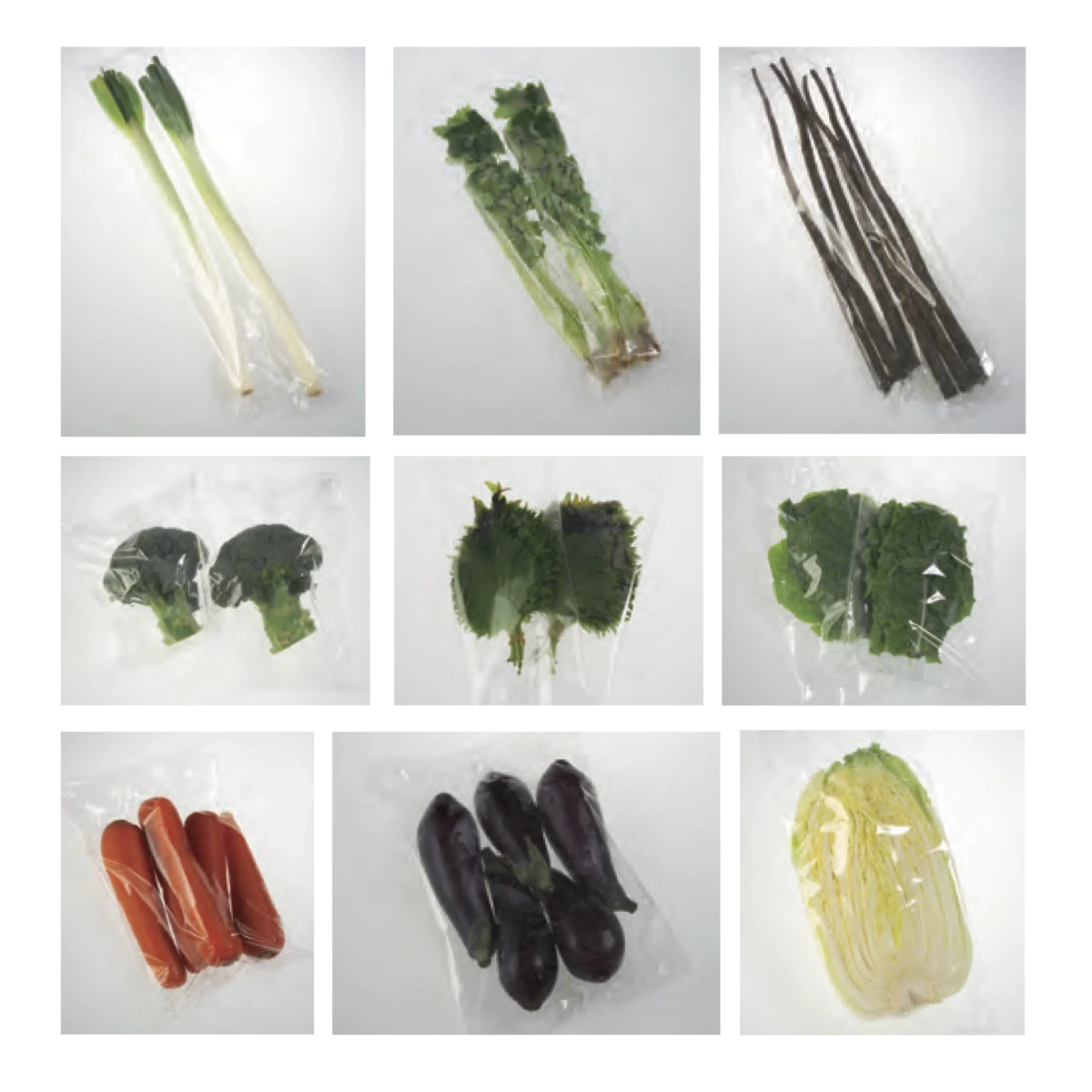
Contact us for more
Our Experts are available to help
- Description
- BENEFITS OF USE
Description
Features
- Adjustable Settings: Flow wrapping machines typically offer adjustable settings for parameters such as wrapping speed, bag length, and sealing temperature to accommodate different products and packaging materials.
- Versatility: These machines are designed to handle a wide range of products, shapes, and sizes, making them suitable for various industries such as food, pharmaceuticals, and consumer goods.
- High Efficiency: Flow wrappers are known for their high-speed packaging capabilities, allowing for rapid and continuous wrapping of products to meet production demands.
- Sealing Mechanism: They feature a sealing mechanism that securely seals the packaging material around the product, ensuring airtight and tamper-evident packaging.
- Ease of Use: Flow wrapping machines often incorporate user-friendly interfaces with intuitive controls for easy operation and setup.
- Durability: Built with robust materials and components, these machines are designed for long-term reliability and durability, even in demanding production environments.
- Safety Features: They may include safety features such as emergency stop buttons, safety guards, and sensors to prevent accidents and ensure operator safety.
- Optional Add-ons: Depending on the specific model and manufacturer, flow wrappers may offer optional add-ons such as printing systems for date coding and labeling, product counters, and automatic feeding systems for increased automation.
While specific benefits may vary depending on the model and manufacturer, the use of a flow wrapper like the Flow Wrap typically offers several advantages for packaging operations:
- Increased Efficiency: Flow wrappers can significantly increase packaging speed and throughput compared to manual or semi-automatic methods. They can wrap products rapidly and continuously, helping to meet production demands efficiently.
- Versatility: Flow wrappers are highly adaptable and can handle a wide range of product shapes, sizes, and types. This versatility makes them suitable for diverse industries such as food, pharmaceuticals, cosmetics, and consumer goods.
- Improved Product Protection: Flow wrapping provides a tight, protective seal around products, helping to preserve freshness, prevent contamination, and extend shelf life. This is particularly important for perishable items and products sensitive to environmental factors.
- Enhanced Presentation: Flow wrappers can create neat, professional-looking packages with consistent seals and appearances, enhancing the visual appeal of the product on store shelves and improving brand image.
- Reduced Labor Costs: Automation provided by flow wrappers can reduce the need for manual labor in the packaging process, leading to cost savings and increased efficiency. Operators can focus on other tasks while the machine handles the wrapping process.
- Minimized Material Waste: Flow wrappers typically use packaging materials efficiently, minimizing waste and reducing packaging costs. Many machines also offer adjustable settings to optimize material usage based on product size and packaging requirements.
- Compliance with Regulations: Flow wrappers can help ensure compliance with industry regulations and standards for packaging, labeling, and food safety. They may incorporate features such as date coding and labeling systems to meet regulatory requirements.
- Streamlined Production: Integrating a flow wrapper into the production line can streamline packaging operations, reducing bottlenecks and improving overall workflow efficiency. This can lead to faster order fulfillment and increased customer satisfaction.
- Scalability: Flow wrappers can scale with growing production demands, allowing businesses to increase packaging capacity without significant investments in additional equipment or manpower.
- Customization Options: Some flow wrappers offer customization options such as printing systems for adding branding, logos, or product information directly onto the packaging material, helping to differentiate products and attract consumers.
These benefits highlight the value that flow wrappers like the Flow Wrap can bring to packaging operations, enhancing productivity, efficiency, and product quality.